LANXESS – Sustainable brine treatment “down under”
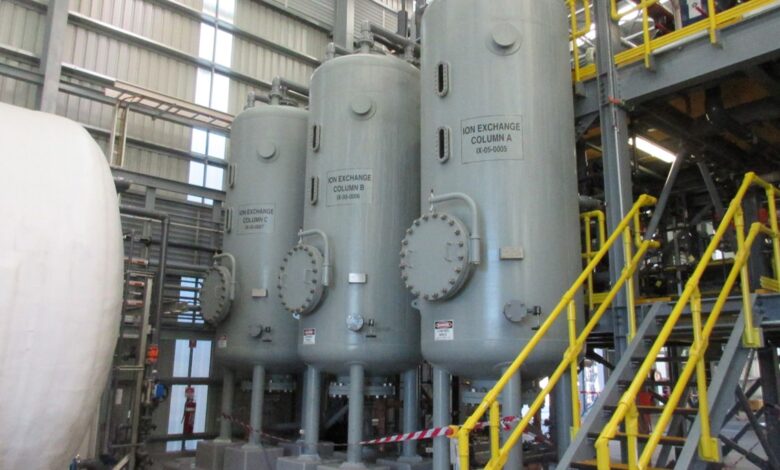
- LANXESS ion exchangers being used for efficient brine treatment in chloralkali facility
- Lewatit MDS TP 208 ion exchanger helps to cut down on wastewater and chemicals
- Successful operation at Coogee Chemicals in Australia
- Lower costs thanks to less waste and longer system service lives
Mumbai, December 28, 2021 – A success story for LANXESS in Down Under: The Lewatit MDS TP 208 monodisperse ion exchanger from the specialty chemicals company is opening up a new approach to a simplified and sustainable sodium chloride brine purification. In Australia, he has been demonstrating his capabilities for half a decade at chlor-alkali producer Coogee Chemicals. It is capable of absorbing a lot more impurities than its MonoPlus equivalent, which means regeneration does not need to take place as often. Lewatit MDS TP 208 makes it possible to cut costs significantly owing to longer cycle times. The process produces less waste and rinse water, which makes it easier to operate a system for chloralkali production. The highly efficient ion exchanger can be relied upon to help meet stringent purity standards.
Proven track record in brine treatment
Coogee Chemicals Pty Ltd is one of Australia’s largest chloralkali producers and operates three production facilities “down under”, all of which work successfully with ion exchange resins from the trusted Lewatit brand. The company’s Lytton site in a suburb of Brisbane has gained an additional state-of-the-art cell room to cover demand for products such as sodium hydroxide, sodium hypochlorite and hydrochloric acid for the chemical industry, water treatment, mining and swimming pool industry. The greenfield project was designed to ensure that the strict regulatory requirements regarding waste reduction could be met reliably, ultimately leading to savings on operational waste and sewage disposal costs.
The amount of waste produced by brine production per year in Lytton is a total of 4,200 m³ lower than in a facility, which uses ion exchange resins with standard particle sizes. That means that the process is helping to conserve precious water resources at the same time. This successful outcome is based on the use of the new Lewatit MDS TP 208 finely dispersed resin, which protects the sensitive electrolysis membranes by reliably removing impurities such as hardness and barium. Since the facility was commissioned in July 2016, it has not only systematically complied with all specifications for brine purity required by membrane manufacturers but also, in some cases, even surpassed them, further boosting the efficiency of the facility in the process.
With the revision of industry standards, the original targets of <300 ug for brine impurities have been cut to less than 100 μg for barium and strontium. By this Lewatit MDS TP208 is giving greater protection to the electrolysis membranes and enables a more energy-efficient operation. Moreover, the pressure loss in the columns of 0.4 bar has remained constant over the entire operational period, changing only when the flow rates are altered.
Since Lewatit MDS TP208 has been adopted into the Chloralkali production process in Lytton, more than five years ago, it has been delivering excellent performance ever since. Because the ion exchange columns are designed for a larger brine capacity, the facility is still capable of extending its treatment volume working with Lewatit MDS TP208 to reach its full potential.