LANXESS developed hot cast/cold cure PU system which saves energy
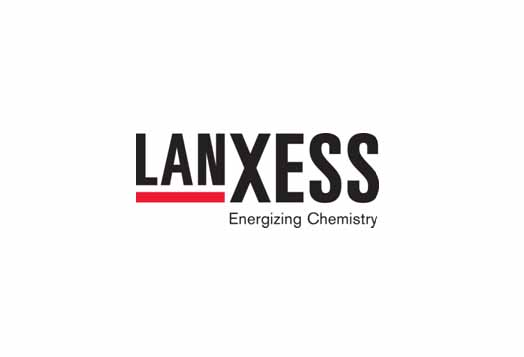
- Novel 3K MDI based PU system from LANXESS
- Significant energy savings, reduced CO2 emissions
- Ease of use and improved EH&S
- Similar elastomer performance as equivalent hot cure system
Mumbai, November 29, 2021 – LANXESS has developed a hot cast and cold cure system for PU cast elastomers. With this new technology, a Vibrathane MDI ether prepolymer can be cured with a novel Vibracure curative at room temperature driving ease of use, energy savings, EH&S improvement and, last but not least, a significant reduction of CO2 emissions.
A combination of ease of use and improved EH&S
As the novel Vibrathane&Vibracure system is cured at ambient temperature, the processor can turn off hot tables or ovens, decreasing significantly the risk of burn associated with hot surfaces and, therefore, improving the operator’s safety. The new MDI ether based prepolymer also facilitates the manufacturing of larger and complex parts such as mining pipelines which curing process is always challenging and productivity limited by equipment occupancy.
Significant energy savings
Energy consumption has always drawn attention from polyurethane processors as it accounts for a significant proportion of the total manufacturing costs. Depending on the polyurethane plant set up, this system can drive savings up to 40 to 50% of the total energy consumption.
Sustainability in focus
The novel Vibrathane & Vibracure hot cast / cold cure system is one of the company’s latest initiatives to enable the PU industry to improve their carbon footprint. Gerald King, Head of Application Technology EMEA at LANXESS Urethane Systems, says: “Sustainability has increasingly come into focus within the last decade and, by driving clear energy savings, with this new development we offer our customers a more sustainable product and thus contribute to climate protection.”
Fully flexible for a wide range of elastomers
The 3K system can be processed by meter mix machine or by hand. It has been chemically designed to offer PU processors full flexibility in producing a wide range of elastomers from a single prepolymer reaching a hardness range from 60 A to 55 D. The cold cure system shows a similar performance in final elastomer properties to the equivalent hot cure.
LANXESS’ new development addresses an important concern of PU processors towards easy processing, cost savings and time efficiency, while allowing the industry to support sustainability objectives.